
Precision engineering is a cornerstone of both the automotive and aerospace industries, where even the smallest components must meet stringent quality and performance standards. One of the most critical processes in manufacturing for these sectors is hydraulic pipe bending. This advanced technology enables the creation of complex, high-strength, and lightweight tubing systems that are essential for vehicle exhausts, aircraft hydraulic lines, and structural components.
Understanding how hydraulic pipe bending technology shapes the future of automotive and aerospace engineering can help manufacturers enhance efficiency, reduce material waste, and improve overall product performance.
The Importance of Hydraulic Pipe Bending in Automotive Manufacturing
Automobiles rely on intricate tubing systems for a variety of functions, from fuel delivery to exhaust emissions. Hydraulic pipe bending plays a crucial role in shaping metal pipes to fit within tight engine compartments while maintaining durability and efficiency.
Applications of Pipe Bending in the Automotive Industry
Exhaust Systems – Modern exhaust systems require precisely bent pipes to optimize airflow, reduce emissions, and improve engine efficiency.
Brake and Fuel Lines – High-pressure brake and fuel lines need to be accurately bent to fit seamlessly into a vehicle’s frame while ensuring safety and reliability.
Cooling and HVAC Systems – Bent pipes transport coolant and air throughout the vehicle, contributing to thermal management and passenger comfort.
Structural Reinforcements – Some vehicle chassis and roll cage components require bent tubing to improve crash resistance and overall durability.
Why Hydraulic Pipe Bending is Preferred in Automotive Manufacturing
High Precision and Repeatability – Hydraulic pipe bending allows manufacturers to produce thousands of identical bends with minimal deviation, ensuring consistency in vehicle assembly.
Material Efficiency – Advanced bending techniques reduce material waste, leading to cost savings and improved sustainability.
Support for High-Performance Materials – Automotive manufacturers use lightweight materials such as aluminum and high-strength alloys, which require precise bending without compromising structural integrity.
Increased Production Speed – Hydraulic bending machines significantly reduce the time required for mass production, improving overall efficiency.
The Role of Hydraulic Pipe Bending in Aerospace Engineering
The aerospace industry demands the highest levels of precision and reliability due to the extreme conditions aircraft components must withstand. Hydraulic pipe bending technology is vital in manufacturing aircraft tubing, which is used in fuel delivery, hydraulic systems, and structural applications.
Key Applications in Aerospace Manufacturing
Hydraulic and Pneumatic Systems – Aircraft depend on extensive hydraulic and pneumatic networks for landing gear operation, flight control mechanisms, and braking systems.
Fuel Transport Lines – Precisely bent pipes ensure efficient fuel flow and prevent leakage, which is crucial for both commercial and military aircraft.
Airframe Structural Components – Lightweight, high-strength tubing is used in fuselage structures, providing both strength and flexibility under varying stress conditions.
Environmental Control Systems – Aircraft heating, cooling, and oxygen distribution rely on complex tubing arrangements that require precise bends to fit within tight spaces.
Benefits of Hydraulic Pipe Bending in Aerospace Applications
Unmatched Accuracy – Aerospace components must meet strict safety and performance regulations. Hydraulic bending machines ensure high precision and compliance with industry standards.
Compatibility with Lightweight Alloys – Aircraft rely on materials like titanium and aluminum to reduce weight while maintaining durability. Hydraulic bending allows for precise shaping of these materials without structural compromise.
Reduced Material Stress and Fatigue – Controlled bending minimizes stress points and ensures the longevity of tubing systems, which is essential for aircraft longevity and safety.
Seamless Integration in Design – The ability to create complex bends allows engineers to optimize space utilization within aircraft structures without sacrificing functionality.
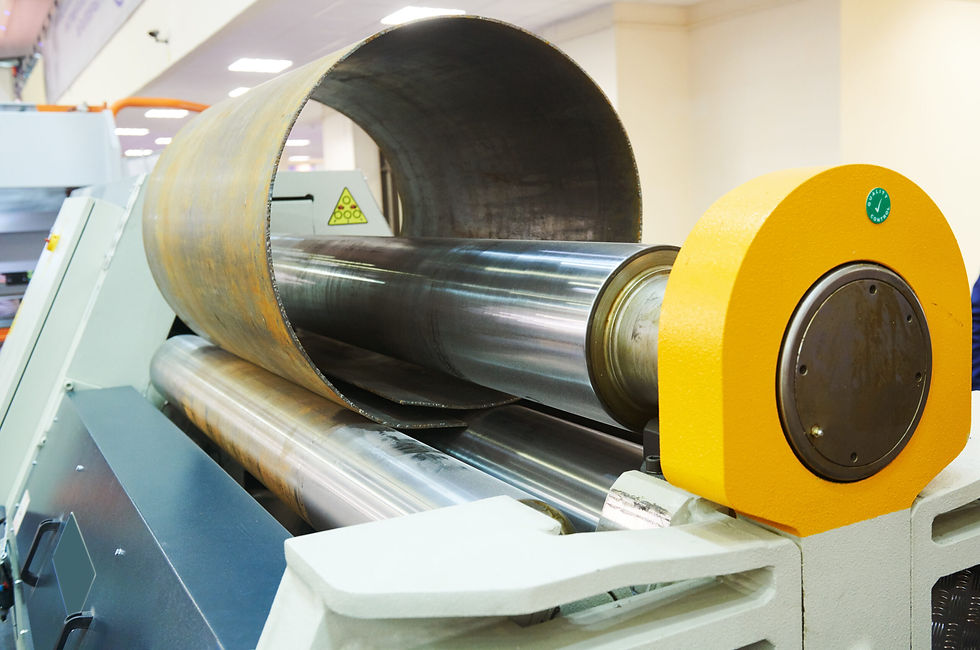
Comparing Hydraulic Pipe Bending for Automotive vs. Aerospace Applications
Feature | Automotive Industry | Aerospace Industry |
Precision Required | High, but allows for slight tolerances | Extremely high, with zero tolerance for errors |
Materials Used | Steel, aluminum, stainless steel | Titanium, aluminum alloys, composite metals |
Production Volume | Mass production of components | Lower volume, highly specialized components |
Regulatory Standards | Industry safety and emissions standards | Strict aviation safety and engineering certifications |
Both industries rely on hydraulic pipe bending for efficiency, precision, and material optimization. However, aerospace manufacturing demands even greater precision due to the extreme environments in which aircraft operate.
The Future of Hydraulic Pipe Bending in Automotive and Aerospace Engineering
With technological advancements, hydraulic pipe bending is becoming even more efficient, automated, and capable of handling advanced materials. Future innovations in this field will likely include:
Integration of AI and Machine Learning – Smart bending systems will use AI to adjust bending force and angles in real time, reducing defects and improving efficiency.
Automation and Robotics – Fully automated bending cells will allow for faster production with minimal human intervention, increasing productivity and accuracy.
Improved Energy Efficiency – Next-generation hydraulic systems will consume less energy, reducing costs and environmental impact.
3D Pipe Bending and Additive Manufacturing – The combination of pipe bending and 3D printing will open new possibilities for lightweight, complex structures in both automotive and aerospace applications.
Choosing the Right Hydraulic Pipe Bending Solutions for Your Industry
Manufacturers in the automotive and aerospace industries require reliable, high-precision hydraulic pipe bending solutions to meet their engineering and safety requirements. Investing in the right equipment ensures efficient production, reduced material waste, and compliance with industry regulations.
PSI Hydraulics specializes in advanced hydraulic pipe bending technology designed for high-performance industries. Whether your business focuses on automotive exhaust systems or aerospace fuel lines, our team can provide tailored solutions to meet your needs.
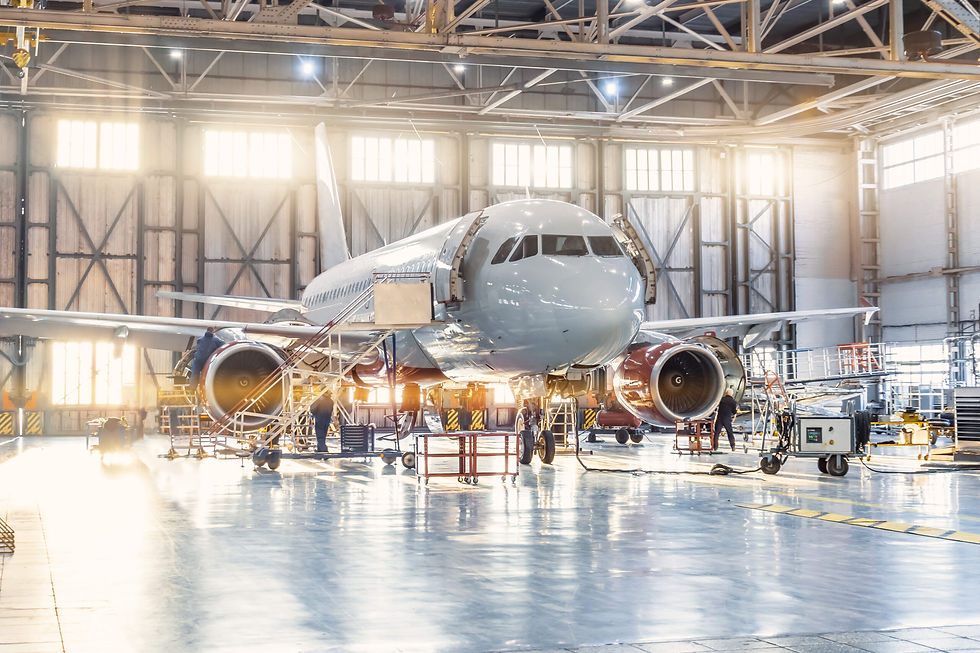
Get Expert Advice from PSI Hydraulics
If you're looking for cutting-edge hydraulic pipe bending solutions for your automotive or aerospace projects, PSI Hydraulics is here to help. Contact us today for expert consultation and precision-engineered bending solutions that meet your industry’s demands.
Comments