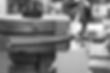
Hydraulic pipe bending is a crucial process in industries such as construction, automotive, aerospace, and manufacturing. It allows for precise bends in metal pipes, making it possible to create durable and efficient piping systems. However, even with advanced hydraulic bending technology, operators often encounter challenges that can affect the quality and efficiency of their work.
Understanding these common issues and knowing how to solve them can help businesses improve their production processes, reduce material waste, and enhance overall performance. This guide explores some of the most frequent hydraulic pipe bending challenges and practical solutions to overcome them.
Pipe Wrinkling and Deformation
One of the most common issues in hydraulic pipe bending is wrinkling or deformation, where the inner wall of the pipe develops unwanted creases or waves. This often occurs when bending thin-walled pipes or when the bending force is not properly distributed.
Causes of Pipe Wrinkling
Insufficient internal support during bending
Incorrect pressure settings on the hydraulic machine
Using a bend radius that is too tight for the pipe material
Excessive friction between the pipe and bending die
Solutions
Use a mandrel to support the inner surface of the pipe during bending
Adjust the hydraulic pressure settings to ensure a gradual and controlled bend
Increase the bend radius to reduce stress on the pipe wall
Apply lubrication to minimize friction and allow for smoother bends
Inaccurate Bend Angles
Precision is critical in pipe bending, but inaccurate bend angles can occur due to machine misalignment, operator error, or inconsistencies in pipe material. Even small deviations can lead to improper fittings and misalignment in piping systems.
Causes of Inaccurate Bends
Improper calibration of the hydraulic bender
Variations in material hardness or thickness
Inconsistent pressure application during bending
Incorrect tooling setup
Solutions
Regularly calibrate the hydraulic bender to ensure accuracy
Use high-quality materials with consistent thickness and hardness
Monitor and adjust pressure settings to maintain control over the bending process
Check tooling setup before each operation to ensure proper alignment and positioning
Springback Effect
Springback occurs when a pipe tries to return to its original shape after bending, resulting in an angle that is shallower than intended. This effect is more prominent in high-strength materials such as stainless steel and aluminum.
Causes of Springback
Material elasticity and composition
Insufficient bending force applied
Using a bending die with an incorrect radius
Solutions
Overbend the pipe slightly to compensate for springback
Use hydraulic benders with controlled force application to minimize rebound
Select a bending die that matches the pipe’s material properties and required bend radius
Test a sample bend before full-scale production to determine the necessary adjustments
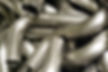
Pipe Flattening
Flattening occurs when the cross-section of the pipe becomes oval instead of maintaining a round shape. This is especially problematic in applications where maintaining a consistent flow of fluids or gases is important.
Causes of Pipe Flattening
Excessive force applied during bending
Lack of internal support for the pipe
Using a die with an improper radius
Solutions
Use mandrels or internal support tools to maintain the pipe’s shape
Reduce the bending speed to allow for a more controlled process
Ensure the bending die is correctly sized for the pipe diameter and wall thickness
Consider using a multi-stage bending process for tighter bends
Cracking and Fracturing
Cracking and fracturing are severe defects that can compromise the integrity of a pipe. This usually happens when bending brittle materials or when excessive force is applied too quickly.
Causes of Cracking and Fracturing
Low ductility materials such as certain aluminum alloys and hardened steel
Applying too much pressure too quickly
Inadequate preheating or improper material conditioning
Solutions
Use heat treatment or annealing techniques to improve material flexibility before bending
Gradually increase hydraulic pressure to avoid sudden force application
Select materials with higher ductility for bending applications
Perform non-destructive testing to identify weak points in the material before bending
Tooling Wear and Tear
Frequent use of hydraulic pipe benders leads to wear and tear of bending dies, mandrels, and other components, which can affect bend quality and machine performance.
Causes of Tooling Wear
Continuous use without proper maintenance
Lack of lubrication, leading to increased friction
Using incorrect tooling materials for specific pipe types
Solutions
Implement a regular maintenance schedule for all bending tools
Use high-quality, durable materials for dies and mandrels
Apply appropriate lubricants to reduce friction and extend tooling lifespan
Inspect tooling before each use and replace worn-out components as needed
Slow Production Speeds
Efficiency is key in hydraulic pipe bending, but certain challenges can slow down the production process. These may include inefficient machine settings, improper workflow organization, or delays in material handling.
Causes of Slow Production
Inefficient machine programming or manual operation
Frequent material changeovers slowing down workflow
Excessive trial and error due to improper initial setup
Solutions
Use CNC or automated hydraulic pipe bending machines for improved efficiency
Optimize material handling processes to reduce downtime
Standardize operating procedures to minimize errors and rework
Train operators to maximize productivity and streamline bending operations
Choosing the Right Hydraulic Pipe Bending Solutions
The success of any hydraulic pipe bending operation depends on selecting the right equipment, materials, and techniques. By understanding and addressing common challenges, manufacturers can improve efficiency, reduce waste, and produce high-quality bends that meet industry standards.
At PSI Hydraulics, we specialize in high-performance hydraulic pipe bending solutions that deliver precision, reliability, and efficiency. Whether you need assistance in troubleshooting bending issues or selecting the right equipment for your application, our team is here to help.

Get Expert Assistance from PSI Hydraulics
If you're facing challenges in your pipe bending operations, let PSI Hydraulics provide the solutions you need. Contact us today for expert guidance, top-quality hydraulic bending equipment, and customized solutions for your industry.